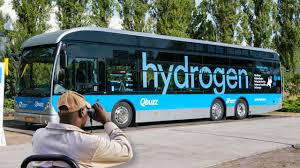
How to Decide on Hydrogen vs. Battery Buses
- Date: October 23, 2024
Zero-emissions buses (ZEB) produce no tailpipe emissions and are primarily powered by hydrogen fuel cells or a series of batteries. This guidebook provides an overview of how battery-electric and hydrogen fuel cell buses work and a comparison of various operational aspects, capital needs, costs, concerns, and safety considerations that will aid agencies in deciding which ZEB technology may work best for them.
Battery-Electric Buses
Battery-electric buses (BEB) are propelled by an electric motor fueled by energy stored in a battery located on the vehicle. BEB charging technology can be plug-in, overhead, or wireless inductive. Plug-in chargers are typically only used at the depot,
while overhead and wireless inductive are used both on-route and at the depot. A charging station typically requires a transformer (often supplied by the utility company), switc
hgear, charger, and dispenser to transfer the electricity f
om the charger to the vehicle. The type of charging infrastructure to select depends on how many miles a bus goes per day, terrain, how often a bus stops, ambient temperatures, available garage space andpower, layover locations, and utility rate costs and schedules.r
Hydrogen Fuel Cell Buses
A fuel cell vehicle uses hydrogen fuel cells as its power source by converting energy produced from the reaction between hydrogen in tanks stored on the vehicle’s roof and oxygen from the air into usable energy. That energy powers the electric motor and a battery that supports auxiliary functions but can also power the motor. Additionally, energy is recovered from braking (regenerative braking) and is also used to provide power to the battery. The only exhaust/waste products produced are water and heat, the latter of which can be recaptured to heat/cool the bus. Vehicles are fueled at a hydrogen fueling station with a dispensing system that delivers fuel to a vehicle (similar to a diesel/CNG fueling station). Hydrogen is either delivered or produced on-site and stored in hydrogen tanks in compressed liquid form.
Comparison of Battery-electric and Hydrogen Fuel Cell Buses
Element | Battery-Electric Bus | Hydrogen Fuel Cell Bus |
Range |
|
|
Capital costs |
|
|
Maintenance Costs |
|
|
Fueling Technology |
|
|
Fueling Infrastructure |
|
|
Scalability |
|
|
Fueling Time and Considerations |
|
|
Facility Needs |
|
|
Safety Considerations |
|
|
Weather Concerns |
|
|